Supply Chain Pressure
The world's ports are facing enormous challenges. The rapid growth in supply chain volumes and ever-larger cargo ships are putting greater pressure on container terminals. The coronavirus pandemic as well as singular events, such as the blockage of the Suez Canal, highlight the fragility of the international supply chain – and the devastating consequences for the world economy when this chain is broken. On top of that, ports also have to comply with growing requirements arising from environmental regulations.he ports themselves, however, have limited room for maneuver, both figuratively and literally.
Around 90 % of the global exchange of goods takes place via the world's seas and ports, and these work like a global marshaling yard that acts as a buffer for other logistics chains. Even if just one part of this network is disrupted, a domino effect is created. In 2020 and 2021, this included the closure of Chinese ports due to the coronavirus, the grounding of the "Ever Given" in the Suez Canal, and the differences in the recovery times of the world's economies. The sudden growth in demand from Western economies resulted in a one-way flow of goods from China, while demand in the opposite direction remained low and consequently disrupted container traffic and shipping. The consequence: a lack of containers, higher logistics costs, a need for more space in ports, and longer jams. Almost all over the world, large container ships are backlogged outside ports, waiting to be loaded or unloaded. The problem, however, is not that handling capacities are insufficient, but that the port storage areas are overfilled. One indicator of this is the so-called dwell time of containers in a port.
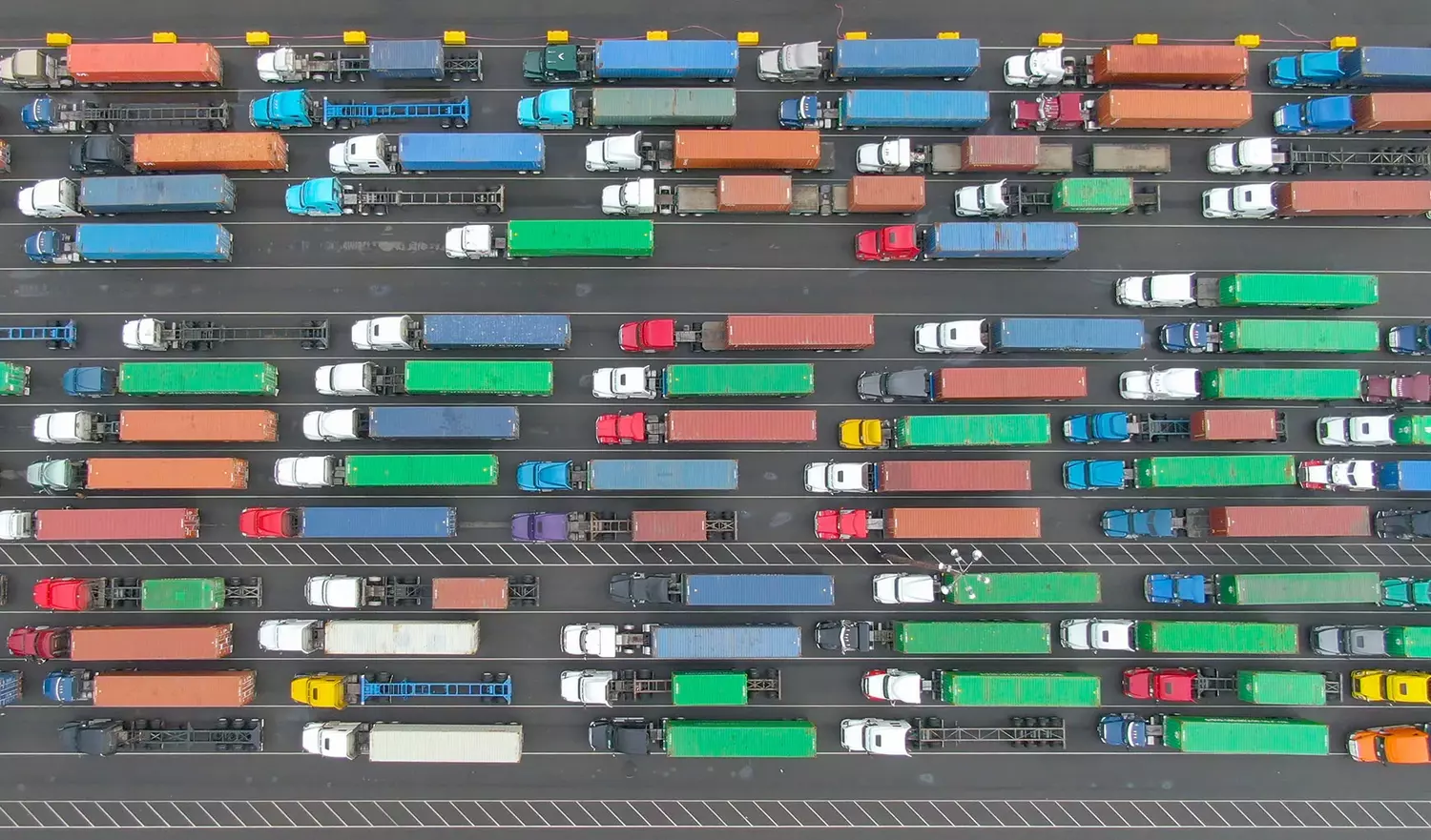
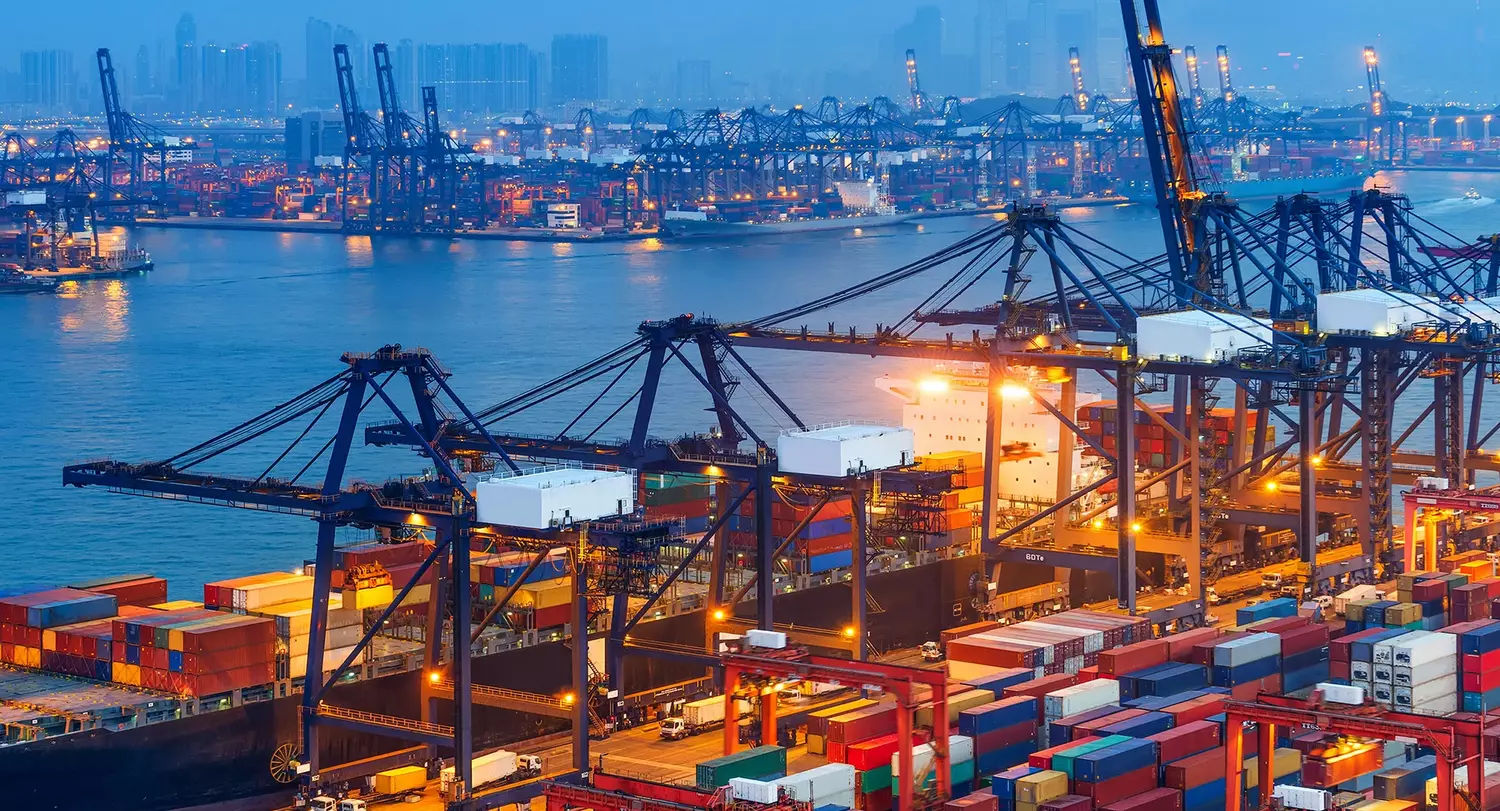
Up to now the reality was a global average dwell time of 3.5 to 4.5 days until a container left a port by truck, rail, or ship. These times have now increased 50 % to 60 %. As a result, the space required is also higher.
What makes the situation more difficult is the fact that bottlenecks also occur during onward shipping by the freight forwarding companies. The containers then remain in the port for longer periods and there is no space available for new incoming containers. All of this is happening against the backdrop of growing container traffic volumes. For years, container growth has been higher than economic growth, but the necessary expansion of port space has lagged behind. At the same time, container ships are steadily increasing in size and the higher capacities and the huge influx of containers that have to be unloaded in docks within a very short time are creating additional storage space bottlenecks.
Challenges in Ports
Challenge 1: Yard Operation
- Large yard footprints
- Containers stacked often 5 to 6 tiers on top of each other, which leads to reduced performance levels once they reach over 70-80 % yard utilization
- Results in big increase in unproductive yard shuffles especially on less predictive landside operations to serve external trucks, trains and barges
- More than 50 % unpaid yard shuffles can occur
- Occupies prime waterfront real estate
- Yard equipment and infrastructure not modular – have to deal with different equipment’s and suppliers
- Warehousing more space intensive and non integrated approach
- In terminal operating systems (TOS), the seamless scheduling of yard strategy (planned a week before vessels arrive) and the equipment dispatch of yard cranes and horizontal transport is one of the bigger challenges
- Reliant on manned horizontal transfer equipment’s (ITV) under qc (hse danger and scheduling)
- Highly labour intensive
- Mean moves between failure (MMBF) interval is low, different types of equipment non electrified/manual- rough handling
- Cfs/lcl warehousing performed by third party
Challenge 2: Not ready for ultra large container ships
- The scale of difficulty increases by having to serve ultra large container ships (ULCS) that require very high service levels with significant peak demands. Waterside productivity requires efficient solutions for faster handling above 200 containers per hour. Most yard operations often struggle to keep up with quay side performance due to the complexity of planned yard strategy and equipment deployment in high utilized container yards.
- ULCS density not in balance with yard density – 8:1 ratio too much space -distances
- Not meeting new waterside productivity demands of 8,000 moves port stay over 20 hours
- Low berth and terminal productivity
Challenge 3: pressure for densification
- Changing liner demands will lead to “industrialized” productions with economies of scale
- Terminal world will be more and more divided in “back-bone” terminals and secondary facilities
- Terminals have to offer predictable performance and high reliability
- Technology application is imperative to manage significant increase of volumes per call and increased peak capacity demand
Challenge 4: insufficient safety & high environmental impact
- Noisy and often polluting port environment due to use of combustion engines
- Yard operation not safe, most of the accidents happen in the yard
- Not pedestrian free – not weather proof
- Highly labor intense – many combustion engines, many staff, risk of injury
- Reliant on manned horizontal transfer equipment’s (itv) under qc (hse danger and scheduling)
- Highly complex and dangerous traffic by mixing internal vehicles with visiting external trucks